Bringing Jobs 'Home' - Political Rhetoric or Economic Reality?
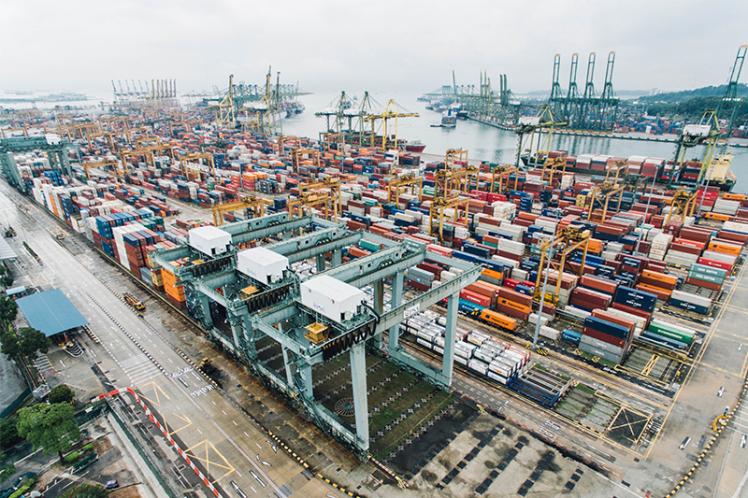
The 2010s have seen an anti-globalization backlash which has gained political expression in the election of Donald Trump in the US, as well as an increasing shift to nationalism in European politics, recently witnessed in the UK's decision to leave the European Union (EU).
Trump used the strapline 'Make America Great Again' in his presidential campaign and, since the election, has been reinforcing his protectionist stance with tariffs mainly (though not entirely) targeted at Chinese imports and the renegotiating of the North Atlantic Free Trade Agreement.
At the same time, the Brexit debate has been continuing in the UK as uncertainty still exists on the final outcome of Theresa May's proposed deal. The main stumbling block to the deal reflects trading realities and borders; the Irish "backstop".
Much of the political rhetoric, especially from Trump, focuses upon reviving jobs in the ‘rust belt’ of manufacturing decay. However, much of the evidence suggests that offshore sourcing still tends to outstrip the jobs that are reshored back to the domestic market.
In the new edition of Logistics and Retail Management, my co-author and I have included a new section on offshore sourcing and reshoring, discussing the topic at length. We argue that the ‘race to the bottom’ continues with companies seeking new areas of low-cost production such as Myanmar, Ethiopia and Haiti as the competitive advantage of China is eroded away by rising costs, long lead times and increased flexibility in a digital age. It is true that the cost gap is narrowing between China and traditional economies but a shift in location will be incremental and is likely to take decades rather than years.
AT Kearney in the US has developed a reshoring index for tracking inward investments. They maintain that the blue-collar jobs lost in the recession in the late 2000s have gone forever and are being replaced with fewer, more technically sophisticated, production jobs. The often-quoted examples of sportswear brands such as Adidas and Under Armour are used as evidence of reshoring, as Adidas, in particular, uses advanced 3D printing to make plastic insoles to customise orders for local markets. It is unlikely, however, that their 90% of physical production from Asia is going to change in the near future.
Another area of concern for companies moving back to the US is the lack of a skilled workforce and an infrastructure capability to produce competitively. Wal-Mart pledged to buy an extra $250 billion of US goods from 2013 to 2023 but has been experiencing difficulties in meeting this target because of the need for upgrading of manufacturing capability.
In the UK the situation is similar. A report last year by Froud and his colleagues at Manchester University ‘ Coming Back? Capability and precarity in UK textiles and apparel’ makes similar comments to the situation in the US. Indeed, it notes that some suppliers have moved into former mill premises in Manchester and Leicester to cater to the fast fashion market. Unfortunately, working conditions and pay rates have drawn media attention to sweatshop conditions normally associated with low-cost economies.
Finally, Brexit negotiations have caused many companies to put on hold their investment plans. Burberry is reinforcing its British roots of the brand by initiating a ‘See -Now, Buy-Now’ strategy which makes available fashion show products as soon as possible after launch. Part of this new approach was to build a new factory at Leeds to manufacture the trench coat to reverse sourcing decisions made a decade earlier. These plans were scrapped in 2017 in view of post-Brexit uncertainty although the company is committed to keeping manufacturing in Yorkshire.